There also a great step-by-step tutorial just above this post. To find it, go to “6152 Project” at the top of this page and look for the drop-down box. There are over 80 images that take you through every stage.
How to build the 6152 step-by-step using the Nightwatch 6152 Case:
This section shows how to shape the top surface of the 6152 Case
Tools: Its possible to do this work with very few tools in fact the 6152 Case in this article was built using only a few files and some wet and dry paper.
Dont I need a Polishing Machine and Dremel? No, you can use these tools of course but I will show you that you can get a better aged finish by not using the Polishing Buffer. As regards the Dremel then it can make life a little easier but its not essential.
Below: These are Medium to fine grade files
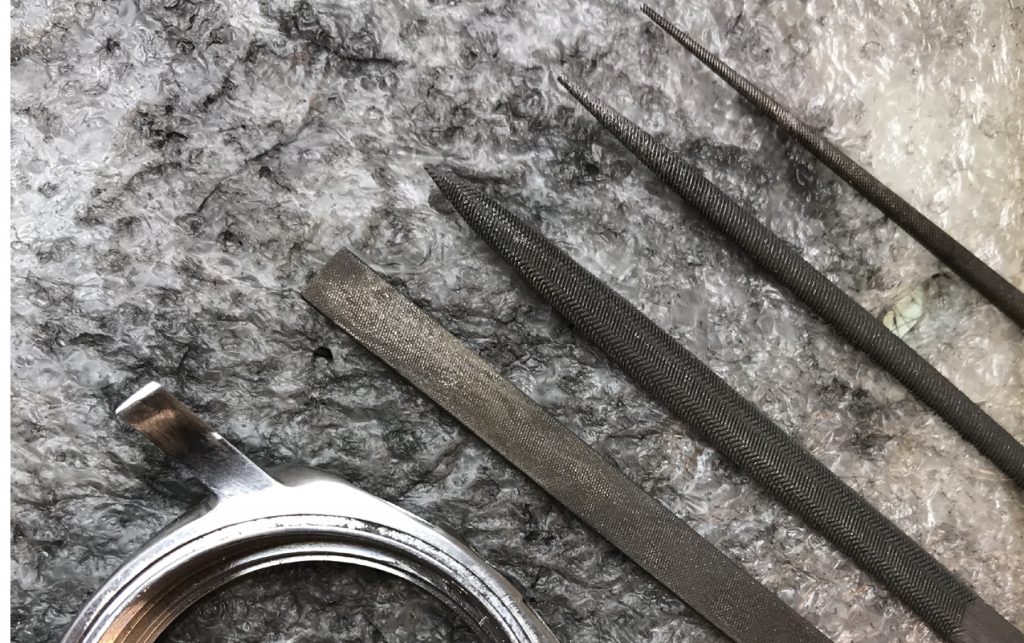
Below: I will use 2 grades of wet and dry paper. Firstly P400 wet and dry paper and then P1200 wet and dry paper
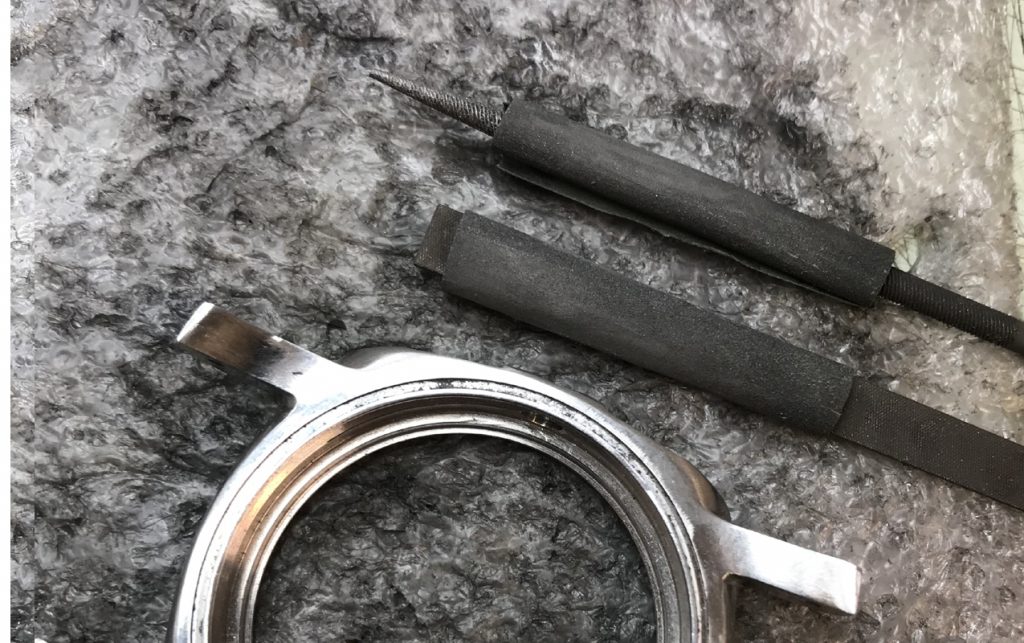
Below: The Dremel is a handy tool for the edges of the case but with a few small Medium to Fine Grade Files I will achieve the same results. In many cases I prefer the files over the Dremel.
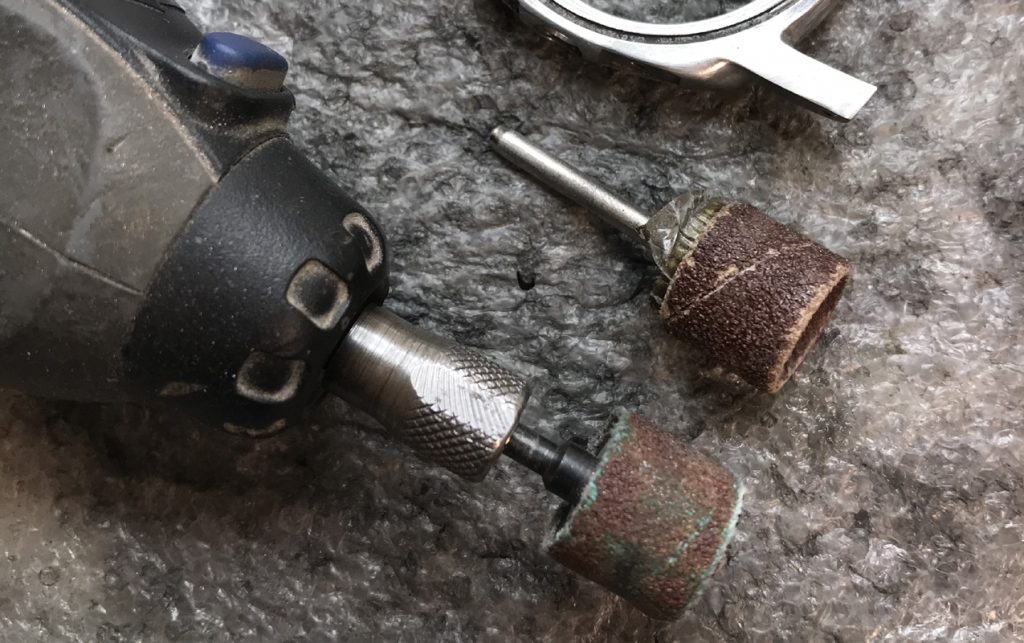
Important: Before we start its important to understand that the 6152 Case is very close to the shape we want to achieve. Therefore you should only be taking small amounts of metal off the case. NEVER take large amounts of metal from an area.
Why shape the case? This is how the authentic Panerai 6152 Cases were made back in the early 1950’s in fact some of the worlds most expensive watches are still finished this way today, its called Hand Finishing. The machinery used back in the 1940/50’s produced a 6152 Case but in order to completely finished the watch case a small team of “finishers” would shape some of the sharp edges and then polish the case. This made the case a little more comfortable to wear and also nicer to look at.
Getting Started: The red arrows below show the areas I will be targeting. These areas do not require a lot of metal removing so be careful. Take your time and remember, its better to take off less metal and correct it later than it is to take off too much metal.
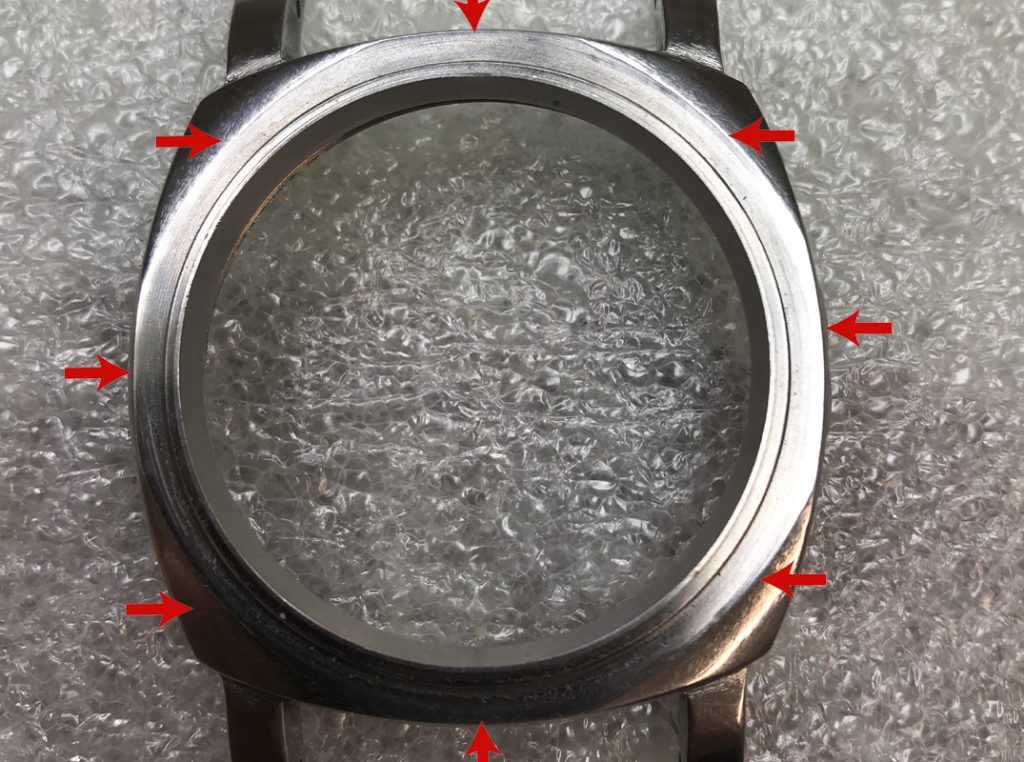
Below: Lets start by smoothing the top surface of the case a little. I have started to file the top surface on the four corners so that they are smooth (see below)
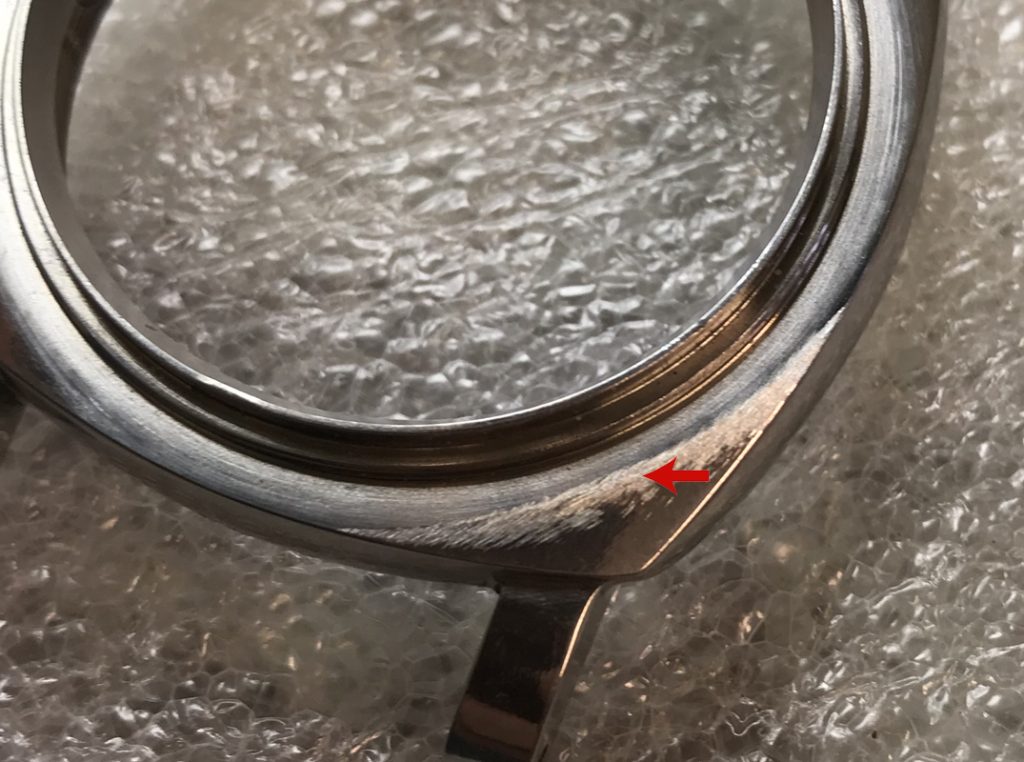
Below: This stage requires the edges to be made smooth around the case.
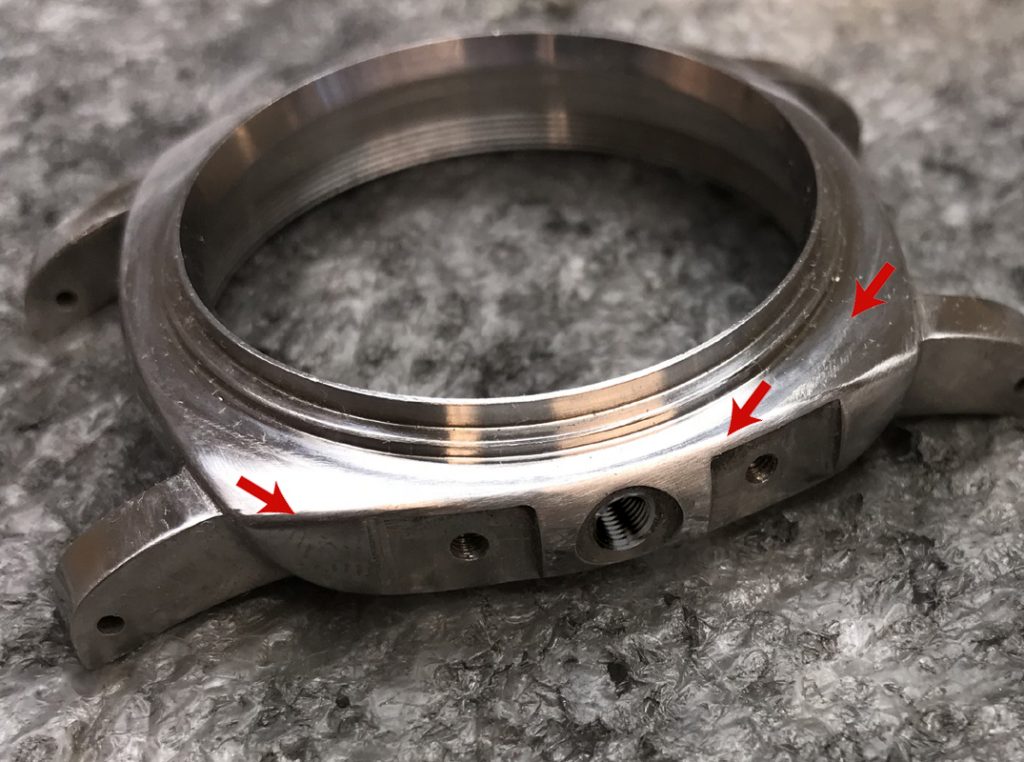
Below: Repeat the process on all sides of the case
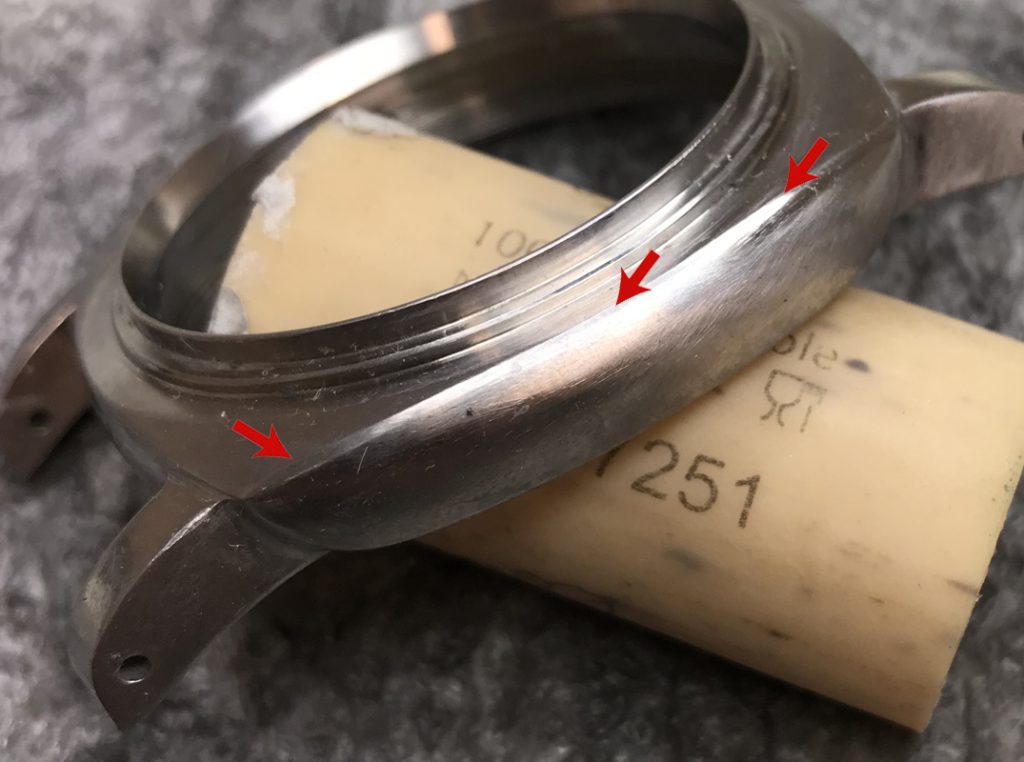
Below: I have added the image below for those that prefer to use the Dremel, This is one job were the Dremel is faster but the same results can be achieved with files. Just be careful not to touch the lugs if you are using the file.
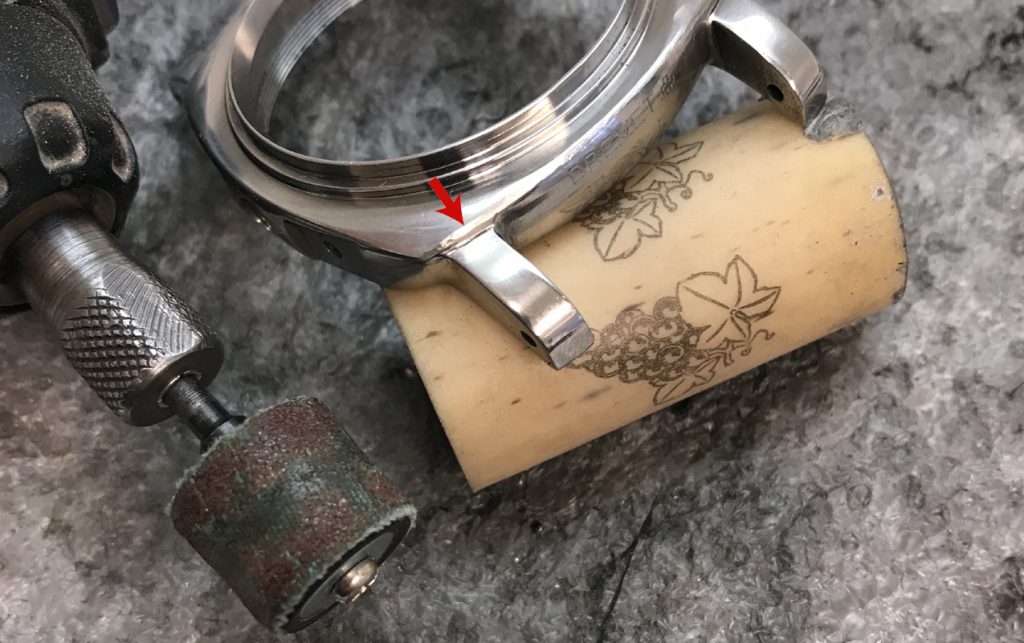
Below: The front edge above the lugs is now nicely rounded and less shape that it was.
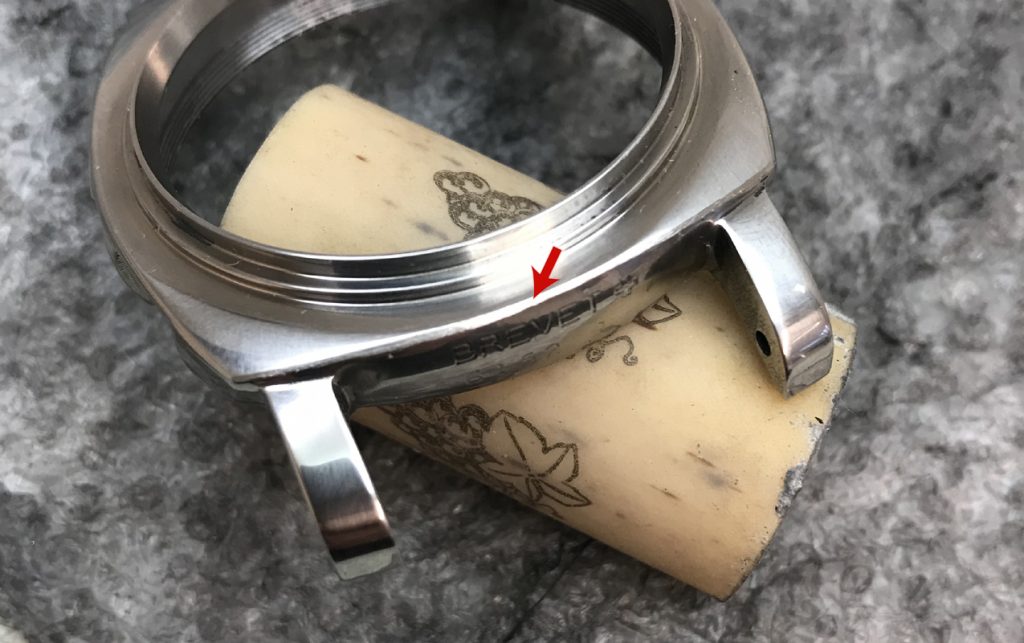
Below: Now go over the area you have filed with P400 wet and dry. Smooth the area until all the scratches have disappeared. If you have used the correct grade file (fine or medium) then this should only take a few minutes. Make sure all scratches are removed.

Below: The font top section of the case is now finished.
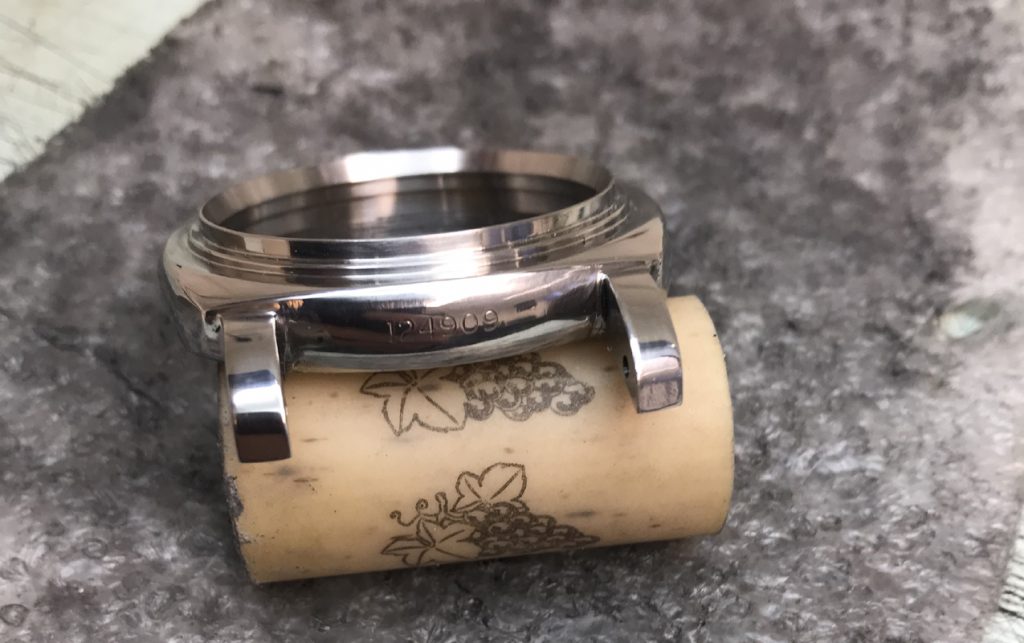